This post will look better on a full sized screen.
I finished the last project on a Saturday night, just in time to catch the last 20 minutes of a Yoshio Suzuki concert at the Mount Fuji Wood Culture Society's chair lab. Yoshio played with Art Blakey, Stan Getz and Sonny Rollins and lived and performed in New York. I felt my fingers and arms and mind, tense from focus on sashimono work, unwind to the music.
The next day, while listening to Suzuki san's Morning Picture album, I started practicing a three-way miter joint in keyaki.
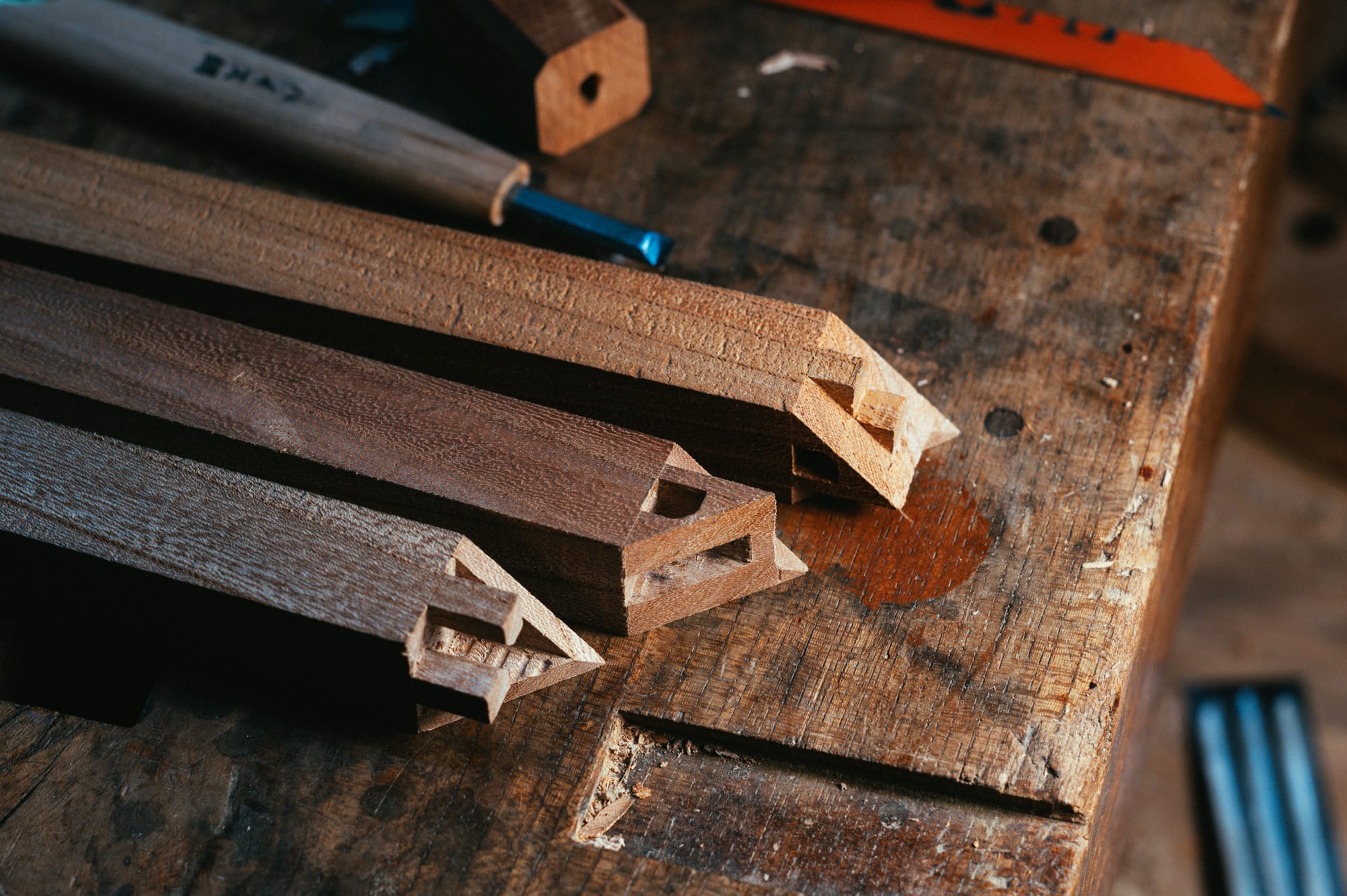
This joint's construction is smaller than the average three-way miter, in stock under an inch thick. Due to my own habit of repeating fundamentals endlessly, I had never cut this joint before. I noticed that the sample joint at the school had partially broken from repeated fitting and disassembly by the students.
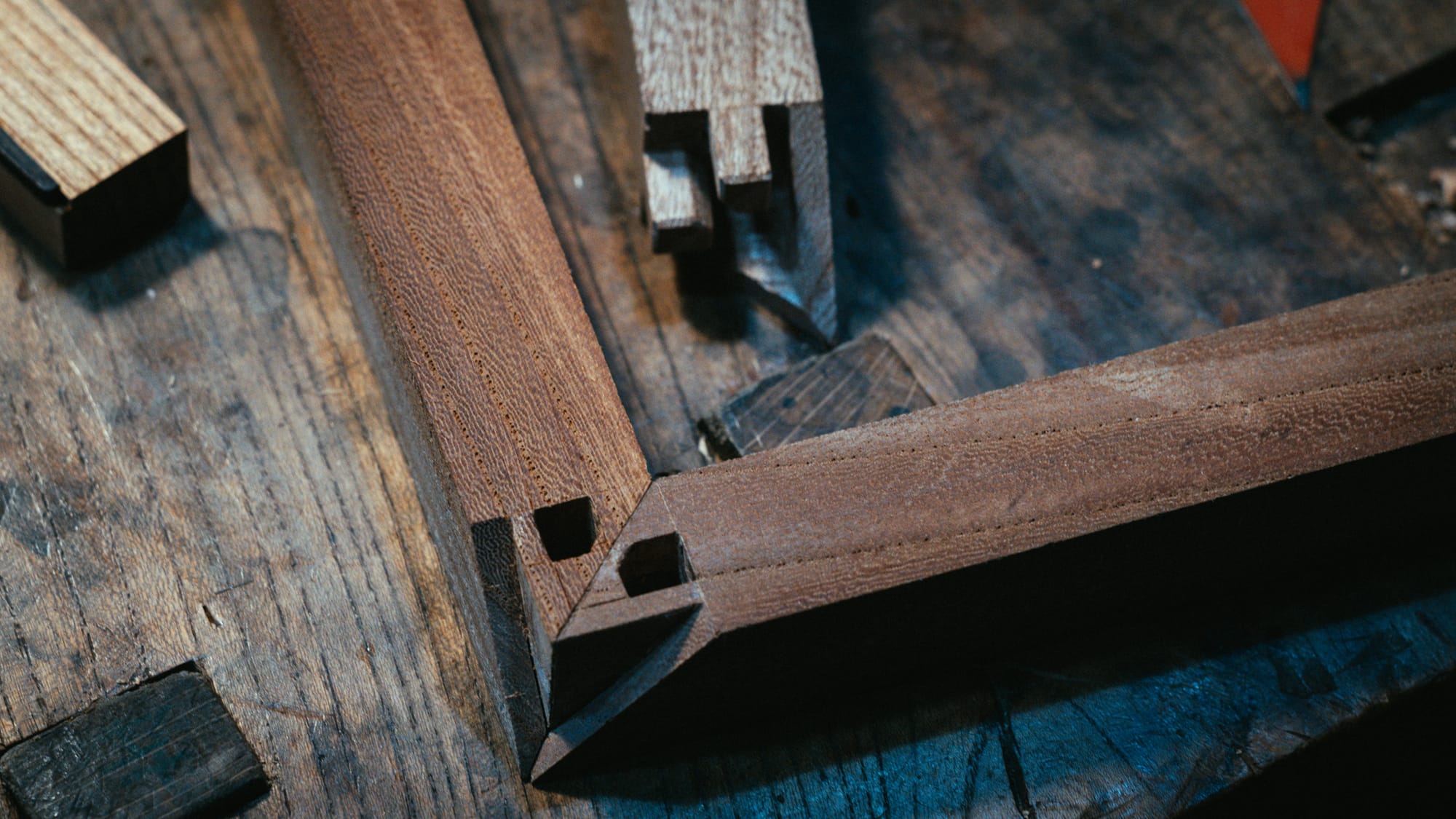
So I modified this one with a heavy chamfer on the corner of the mortise where it ran close to the miter. I also tapered the tenons along this chamfer, so that the joint would draw the other two pieces together as it fit. It worked well enough that it was almost impossible to disassemble. The three-way miter is For all my fear of this joint over the last half decade, it was not too bad to cut.
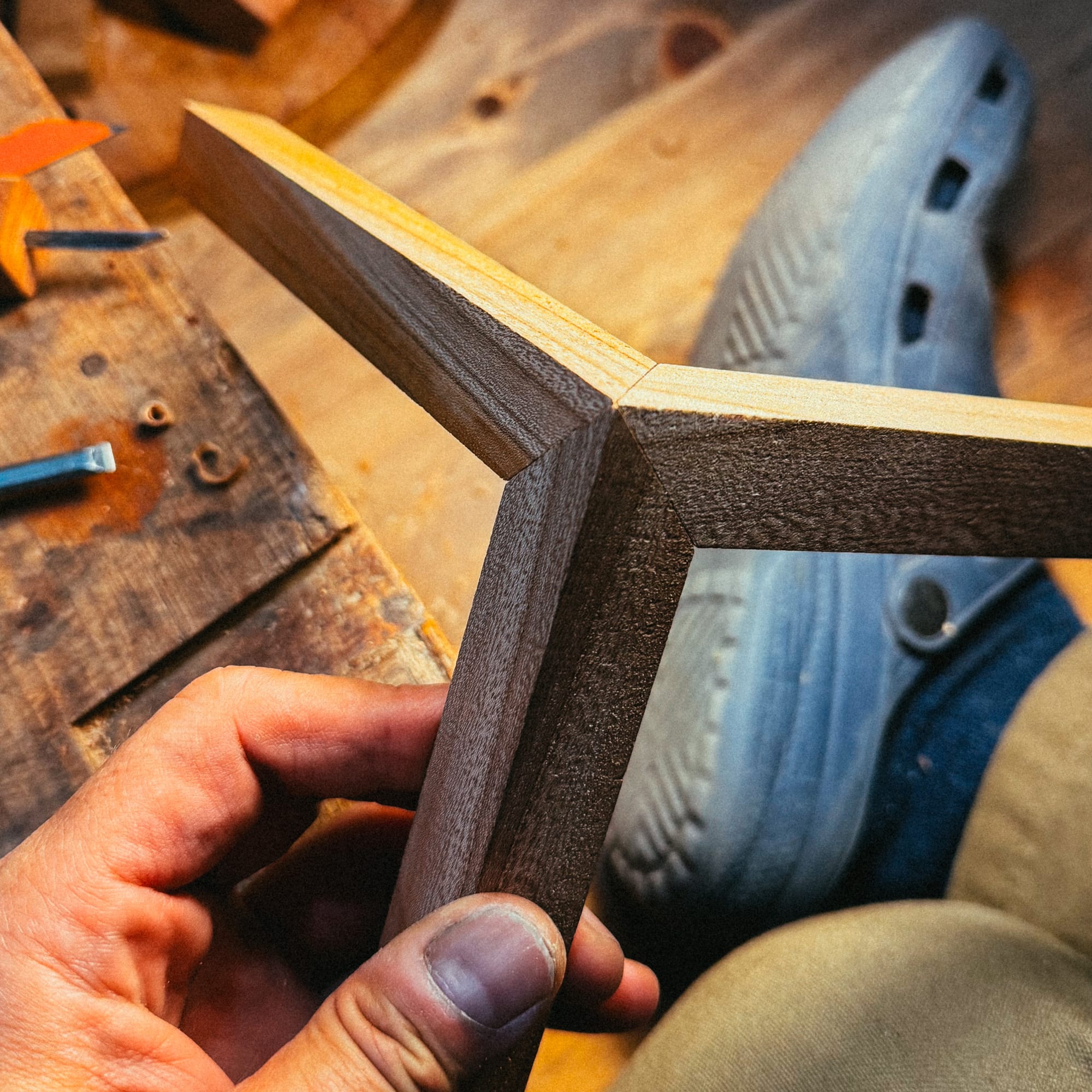
So far, my tests had gone well. By this time in the residency—about ten days in, with ten days left—I was running out of time to only practice. I needed to start on a more ambitious project. I was having difficulty knowing what to do next and feeling demoralized. At this point in a student's studies, I should copy masters according to 守破 離 (Shu Ha Ri) learning principles, not designing my own pieces yet. I was also starting to miss my daughter.
And, from sitting on the floor at Suda Kenji's old atedai, my 47-year old body started to ache. Some enthusiastic new students filled the shop, and due to some project deadlines, the machines were also running morning to late night. A bit overstimulated, I retreated to my room with a pile of books to figure out what to build next.
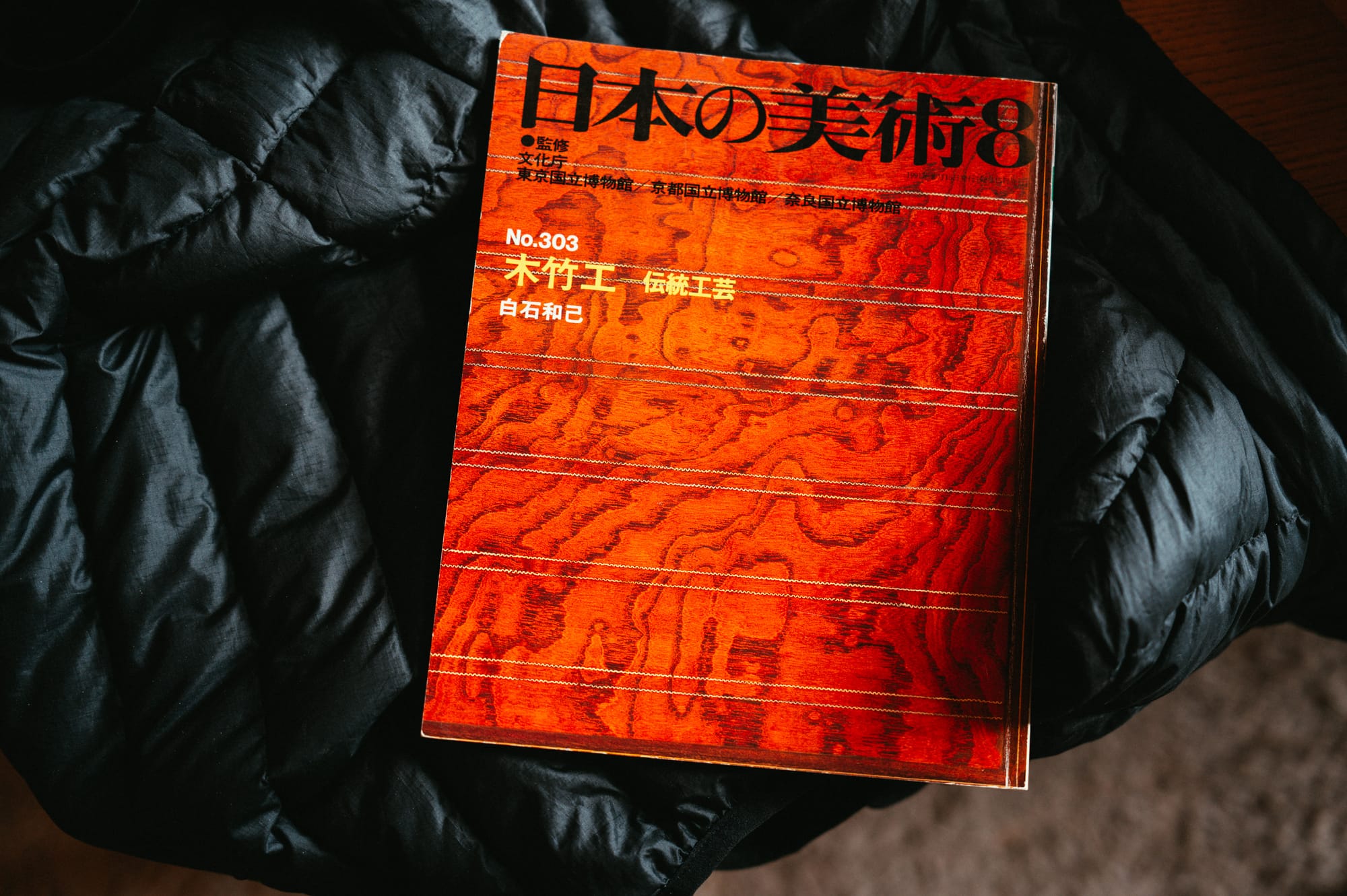
I learned that this was not all an uncommon feeling. Traditional sashimono from this lineage have had a habit of working from 4pm to 4am, to avoid distractions.
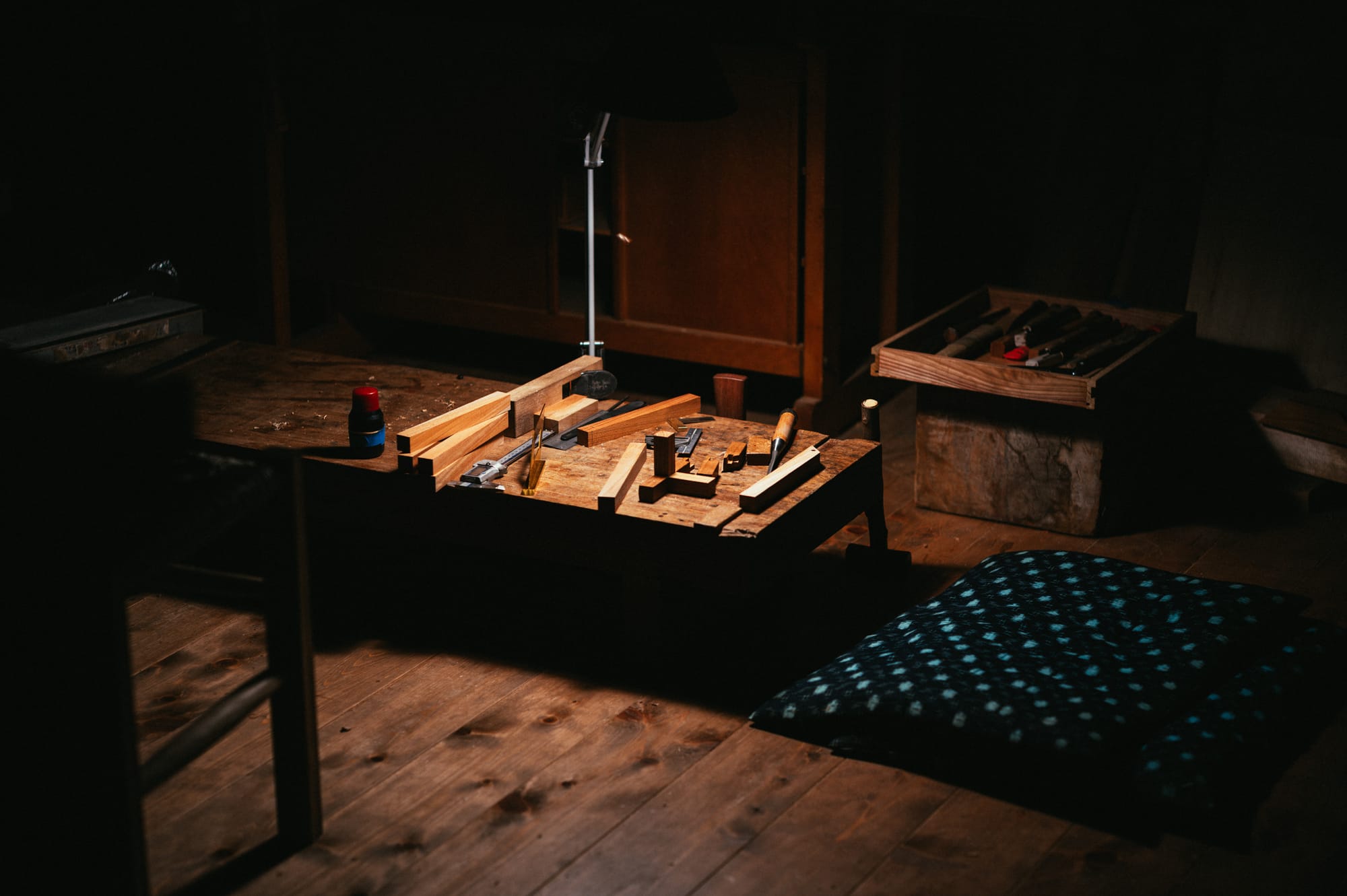
No matter what, I could sneak down late in the quiet night to work alongside Togo, who was working on casework for his craft exhibition piece.
One night, flipping through an old magazine that Suda san had given Tak san, I found a beautiful small table.
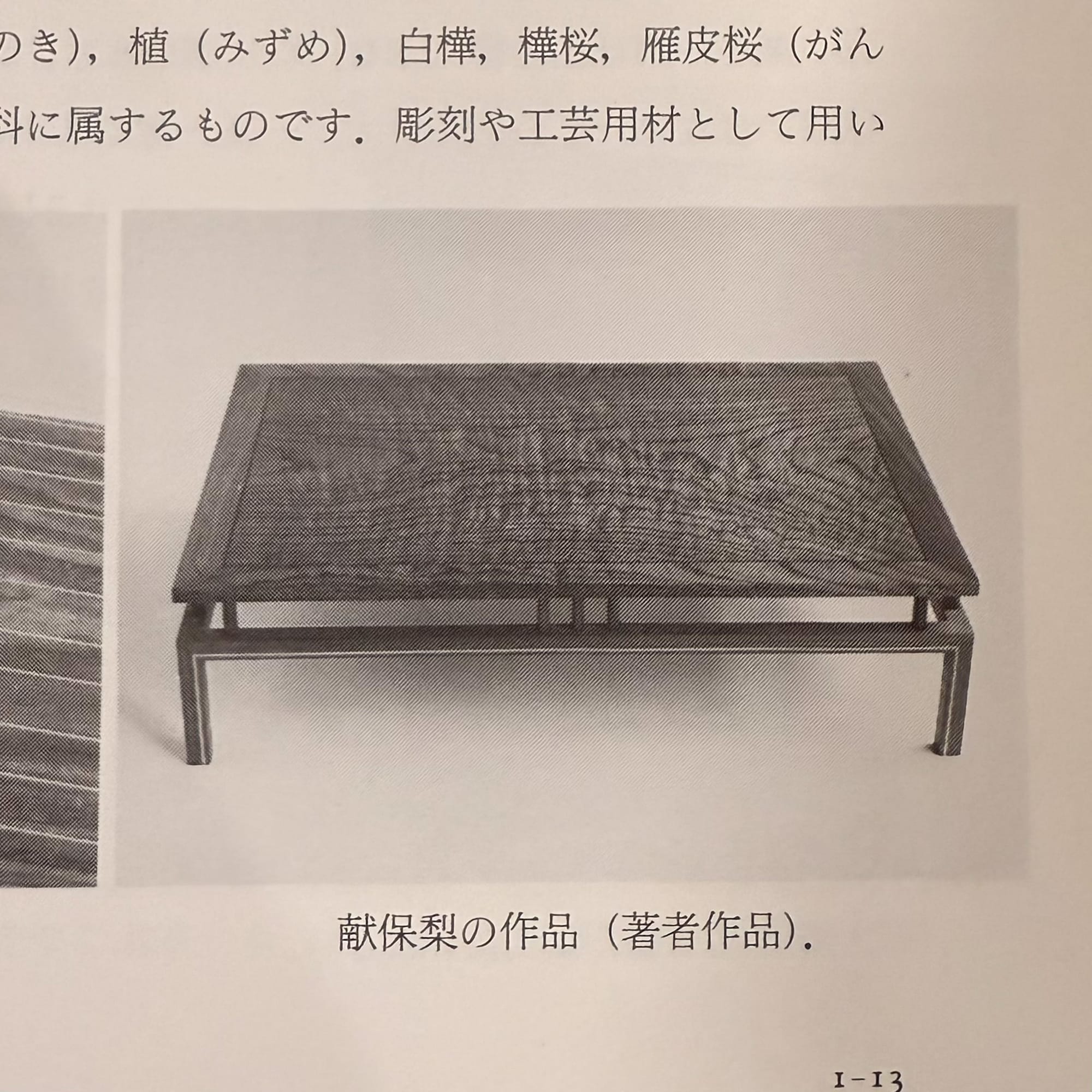
Tak later told me it is a table used to carry burning incense called a 平卓 (hirataku). Instead of this two-level table, he suggested I try a different table with fewer parts but a more tricky corner detail between different-sized parts.
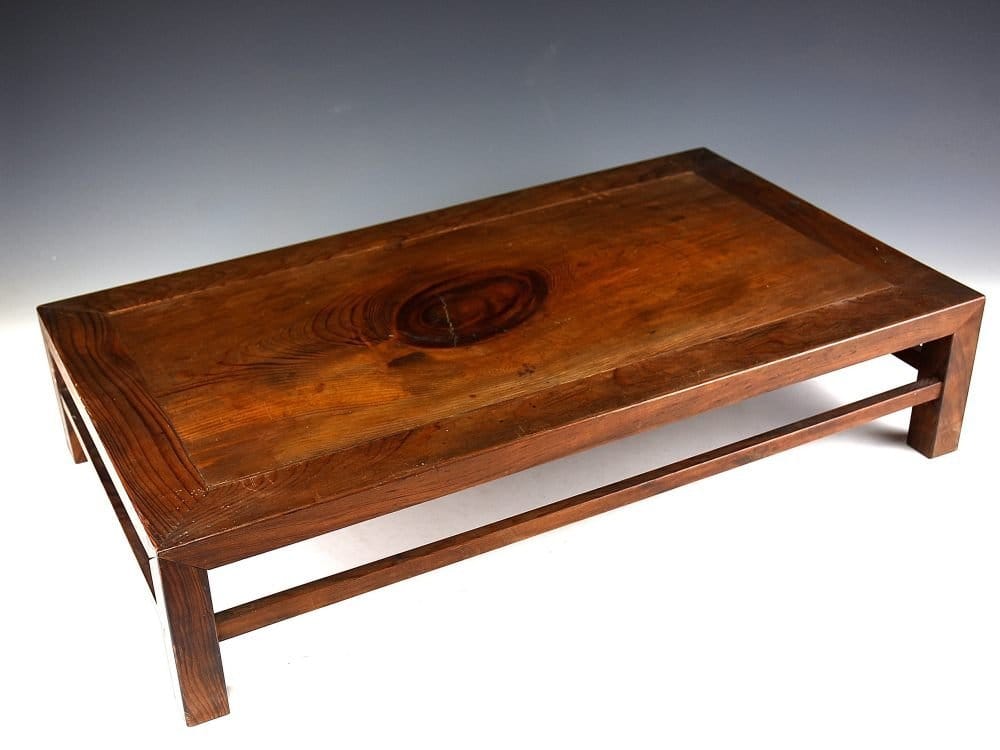
He said he had seen this kind of table in 15mm leg thickness before, so he knew it was possible. I told him that I already cut my leg material in 12mm thickness, so I would try to do it in that stock, making the project more difficult.
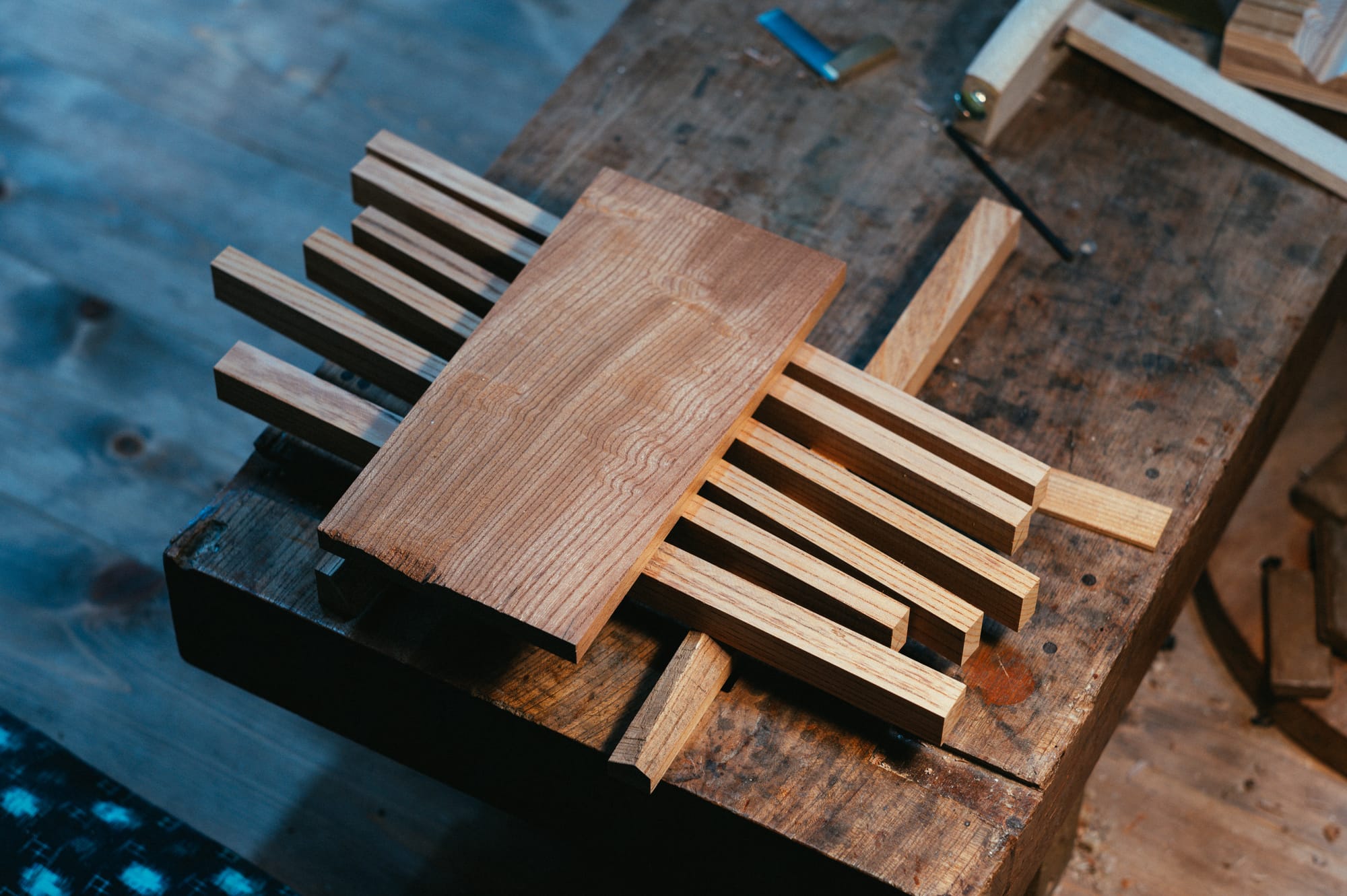
To make my frame joint more accurately, I first rough-milled the wood and let it sit for a day before doing final milling.
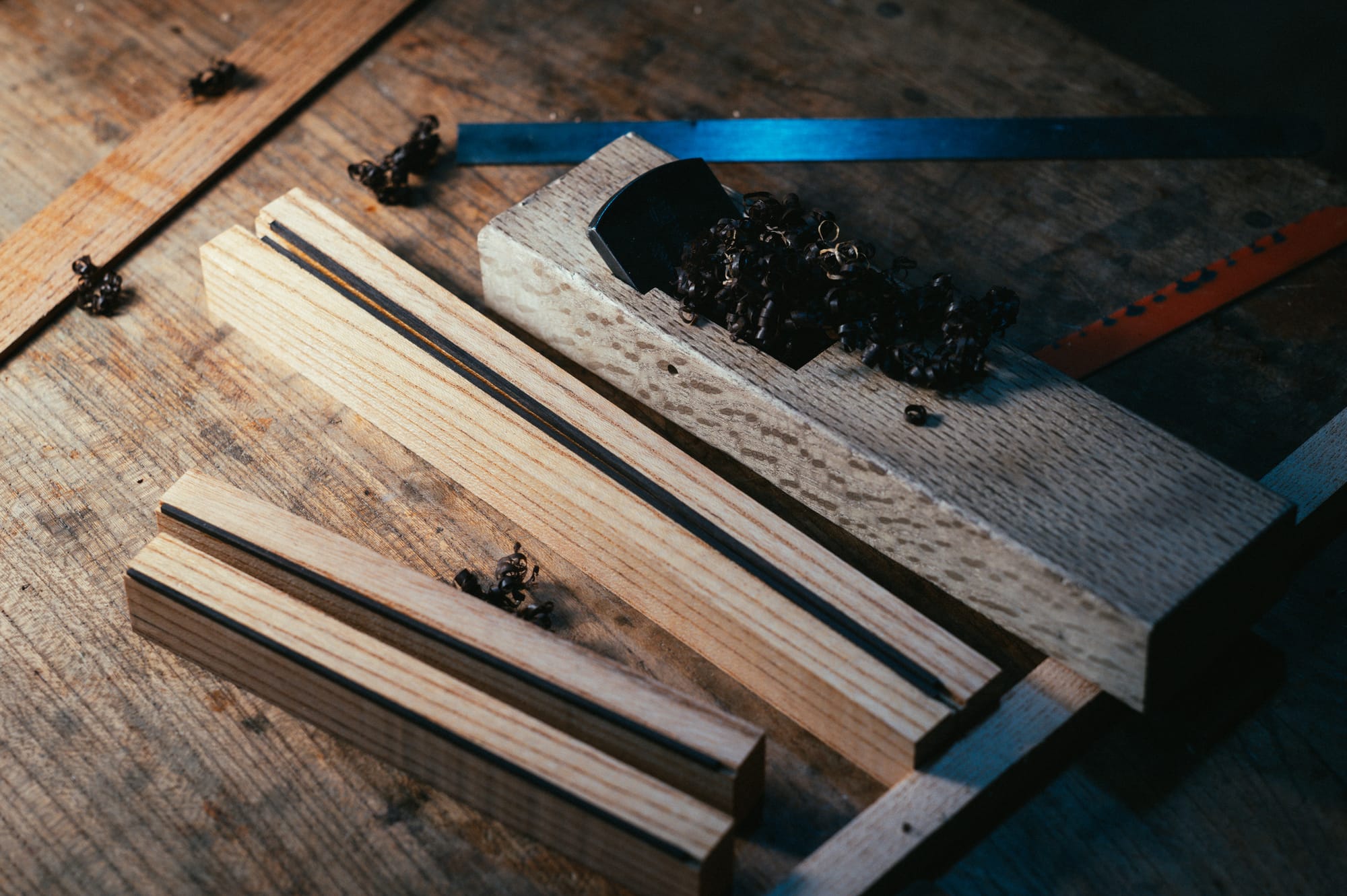
Then I super-glued some ebony inlay into rabbets, finished by kiwa-kanna (rabbet planes). Matching the grain of the ebony and the keyaki frame pieces, I planed the ebony flush to the surface of the keyaki using a brass-mouthed high-speed steel small plane.
It was time to cut the mortise and tenons frame pieces.